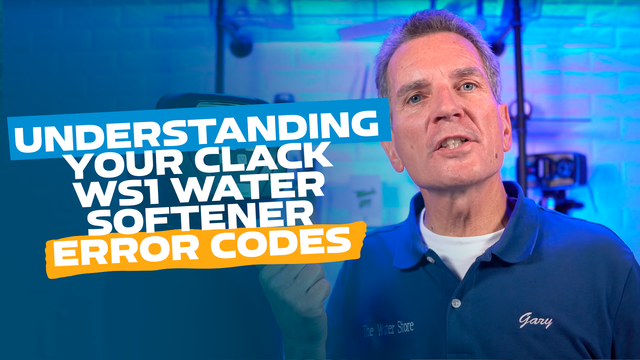
Is your Clack water softener showing an error code? Well, we have good news and bad news. The bad news is that your water softener isn’t working. But the good news is that the error code is going to tell us exactly what’s wrong and how to fix it!
If you know how to interpret those codes, you can repair your water softener like a pro. It doesn't matter if it's a water softener or an iron filter, the codes and the remedies are all the same. The odds are very good that this is a relatively easy fix and something you can do yourself. You probably don’t need to call in a technician to diagnose and solve the problem.
The error codes and the remedies that we’ll be discussing today apply specifically to the Clack WS1 valve. There are a number of companies that use this valve. We use it for our HUM Water Filtration products, but it’s also used by companies like Water Depot and Viqua.
They all use the same valve. The face plates may look different, but you can spot a Clack valve by looking at the top of the valve. The bypasses are often red, with the ends flared out like an arrow.
If you need a visual aid, just click on this video.
Is This Error Just a One-off Glitch?
Sometimes your error is just a glitch in the system and you can simply fix things by clearing the error code. To do that, you’re going to open up the faceplate and unplug the power source, which is the white cord on the bottom right of the circuit board. You should leave it unplugged for at least 5 seconds, but we like to give it 30 seconds just to be on the safe side. After you plug it back in, it's going to go through its startup procedure, and when it’s done, it will clear the error code.
That may solve the problem.
Clack WS1 Water Softener Error Codes Explained
Error Code 1001 – (or E1, Err 101): Unable to recognize start of regeneration
There is an optical eye behind the circuit board that senses where the valve is. If you’re getting this error, the eye can’t see.
The Remedy: Most likely something is blocking the reflective tape. You can remove the circuit board, take out the little discs and just make sure that everything is clean, then reassemble it.
It could also be that the motor isn't working or isn’t seated properly. The motor has a little spring clip and if you pull that clip, you can pull the motor out. Make sure that the motor’s all the way in and make sure the board is snapped into place.
You will get that same error code if you have a defective circuit board because the optical sensors are part of that board.
Error Code 1002 – (or E2, Err 102): Unexpected stall, unable to find next cycle
What's an unexpected stall. The valve is trying to go to the next cycle, but it can't because something is binding it or blocking it from going to that next cycle. The most common scenario is that something is actually stuck within the valve.
Your valve contains a seal pack and a piston. The tolerances are very tight. If you have a lot of iron in your water, it can build up in that basket and bind your piston.
The Remedy: You can solve this problem by opening up the valve, disassembling it, and cleaning it out. Want to see how to do it? We walk you through in this video.
Once you’re done that, you will need to resync your valve by unplugging the power cord again for 5-30 seconds. You will actually have to do that after most troubleshooting steps. If it's not okay after that, you may need to replace the piston and the seal pack.
Some of the other causes may include the main drive gear being too tight. That typically happens when you've done some service on this and you've just tightened it too much when closing it up.
At the same time, the wrong voltage could cause the same problem. You need to check that you've got the correct voltage going in, and ensure there isn't an issue with the hydro in your home, cottage, or cabin.
Error Code 1003 – (or E3, Err 103) – Motor ran too long, timed out
Your motor timed out trying to reach the next cycle. What could be causing that motor failure? Is it time to replace the motor? To be honest, it's very seldom that the issue is a motor failure. We’ve been working on these valves since 2003 and we’ve only ever replaced one motor. It's pretty rare.
It’s more likely that you have a build-up of sand or iron in the piston. We talked about that a little bit earlier with the error code 2002.
You might also be dealing with the drive bracket not being properly snapped in place. Once again, when you're reassembling it after disassembly, just be careful the wires don't interfere and make sure that you’ve pressed it all the way back into the housing. You should feel it snap into place. If it doesn't snap into place, it will cause you grief. And once again, make sure you resync it.
Error Code 1004 (or E4, Err 104) – Control valve motor ran too long
This is almost certainly because the motor valve is not snapped into place properly. As we mentioned earlier, if it’s not secure, you’re going to run into all sorts of problems.
The Remedy: Make sure it’s snapped firmly in place, then resync the valve when you’re done.
Error Code 1006 – (or Err-116, Err 106) – Valve not recognizing MAV
This one is telling us that the valve is not recognizing the MAV. MAV stands for Multiple Valves System. Most likely, someone (probably on the factory side) has made a mistake in the programming. They have defined that this valve is supposed to work with a MAV. But in this situation, that's not the case.
The Remedy: You need to reprogram it, using this helpful video.
Error Code 1007 – (or Err-117, Err 107) Foreign matter is lodged in MAV causing mechanical binding
This is possibly the same problem as above. You may get this error if you don’t have a MAV, but you seem to be programmed for one. Or it’s possible that you do have a MAV, but it’s dirty.
The Remedy: Once again, if you don’t have a MAV, you can reprogram your unit using this helpful video.
If you do have a MAV, you need to open up the MAV, clean it out, find out what's causing the blockage, put it back together, and resync it. That should resolve the issue.
Check out our Clack Water Softener Error Codes video here
We’re Here For All Your Water Softener Needs
As you can see, none of these error codes mean that you need a new water softener, which is a good thing!
But if you do, we recommend something like our HUM Metered Water Softener System 30,000 Grain Capacity, or our AQUAMASTER AMS 700 High-Efficiency Water Softener.
Of course, if you have any questions, you can contact us by clicking here.